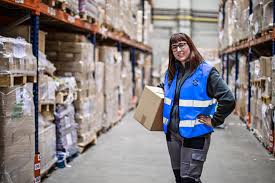
In the dynamic landscape of logistics and supply chain management, efficient warehouse operations are critical to meeting customer demands, reducing costs, and driving business growth. Third-party logistics (3PL) providers play a pivotal role in optimizing warehouse processes by leveraging advanced technologies and expertise in supply chain management. This article explores how top 3PL providers are revolutionizing warehouse operations to streamline processes and enhance overall efficiency.
Section 1: Importance of Warehouse Optimization
Warehouse optimization is essential for businesses to meet the increasing demands of modern consumers and achieve operational excellence. Key benefits include:
- Enhanced Efficiency: Optimized workflows reduce bottlenecks and improve resource utilization.
- Cost Reduction: Streamlined operations minimize labor costs, inventory holding costs, and space utilization.
- Improved Customer Satisfaction: Faster order processing and accurate inventory management lead to superior customer experiences.
- Scalability: Efficient warehouses can scale operations seamlessly to accommodate growth.
Section 2: Role of 3PL Providers in Warehouse Optimization
Leading 3PL providers specialize in warehouse optimization by offering:
- Advanced Technologies: Integration of IoT, robotics, and AI-driven analytics for real-time monitoring and predictive insights.
- Optimized Layout Design: Efficient storage configurations and layout planning to maximize space utilization.
- Inventory Management: Inventory optimization strategies to minimize stockouts and excess inventory.
- Order Fulfillment: Streamlined picking, packing, and shipping processes for faster order turnaround.
- Supply Chain Visibility: Enhanced visibility through track-and-trace technologies for end-to-end supply chain transparency.
Section 3: Case Studies: How Top 3PL Providers Optimize Warehouses
Case Study 1: IoT-Driven Inventory Management
Provider: Logistics Innovations Inc.
Challenge: Inefficient inventory tracking leading to stockouts and excess inventory.
Solution: Implementation of IoT-enabled inventory tracking system.
Outcome:
- Achieved 99% inventory accuracy.
- Reduced stockouts by 25% and excess inventory by 15%.
Details: Logistics Innovations Inc. faced challenges with inaccurate inventory tracking, resulting in frequent stockouts and excess inventory accumulation. To address this, they implemented an IoT-enabled inventory tracking system that utilized sensors and RFID technology.
The IoT system continuously monitored inventory levels in real-time, providing accurate data on stock movements and storage conditions. This level of visibility enabled precise inventory management, leading to a 99% accuracy rate in inventory tracking. As a result, Logistics Innovations Inc. significantly reduced stockouts by 25% and excess inventory by 15%, optimizing warehouse space and minimizing carrying costs.
Case Study 2: Robotic Automation in Fulfillment
Provider: Smart Logistics Solutions
Challenge: Manual order picking inefficiencies impacting order fulfillment speed.
Solution: Deployment of robotic picking systems.
Outcome:
- Increased order fulfillment speed by 30%.
- Reduced labor costs by 20%.
Details: Smart Logistics Solutions identified manual order picking as a bottleneck in their fulfillment process, leading to slower order processing times and higher labor costs. To address this challenge, they introduced robotic picking systems into their warehouse operations.
The robotic systems were integrated seamlessly into the existing fulfillment process, automating repetitive picking tasks and improving overall efficiency. With the deployment of robotics, Smart Logistics Solutions achieved a 30% increase in order fulfillment speed while reducing labor costs by 20%. Employees were able to focus on more value-added tasks, further enhancing productivity and operational efficiency.
Case Study 3: AI-Powered Demand Forecasting
Provider: Supply Chain Dynamics
Challenge: Inaccurate demand forecasting leading to overstock and understock situations.
Solution: Adoption of AI-driven demand forecasting tools.
Outcome:
- Improved demand forecast accuracy by 25%.
- Reduced excess inventory by 10%.
Details: Supply Chain Dynamics struggled with inaccurate demand forecasting, resulting in frequent overstock and understock situations that impacted inventory management and operational costs. To address this challenge, they adopted AI-driven demand forecasting tools powered by advanced machine learning algorithms.
The AI-powered forecasting tools analyzed historical sales data, market trends, and external factors to generate more accurate demand predictions. As a result, Supply Chain Dynamics improved their demand forecast accuracy by 25%, reducing instances of overstock and understock. This optimization led to a 10% reduction in excess inventory levels, optimizing working capital and improving overall warehouse efficiency.
Conclusion
Warehouse optimization is a key strategic initiative for businesses seeking to streamline operations and drive competitive advantage. By partnering with top 3PL providers and leveraging innovative technologies, organizations can achieve greater efficiency, cost savings, and customer satisfaction in their supply chain operations.